Software design service for automation
Our extensive experience in the field of industrial automation has naturally evolved into software development.
Specifically, the software design is carried out in an internal department within the company, allowing us to meet all customer requests and achieve the desired results. By utilizing the most advanced technologies, we develop software applications for industrial automation on PC, PLC, SCADA, and HMI platforms, depending on various requirements.
This activity is carried out by highly qualified personnel who, working within the company and/or at the final client’s site, are responsible for designing software for:
- Creating the human-machine interface (HMI)
- Commanding and controlling machines, production lines, and automatic warehouses
- Upgrading existing production lines or machines to bring technological modernization
- Developing interconnection and communication between systems of multiple plants, stations, production lines, and management environments (MIDDLEWARE)
- Controlling execution and tracking the assembly operations of automotive and industrial components
- Controlling processes and evaluating the characteristics of mechanical or hydraulic components (TEST BENCH)
Based on a development process that includes acquiring and analyzing customer specifications, studying and creating the application, conducting a series of in-house tests, commissioning at the site, and final production testing, we can validate the project in full compliance with the contract requirements.
Automatic Screwdriving System Control
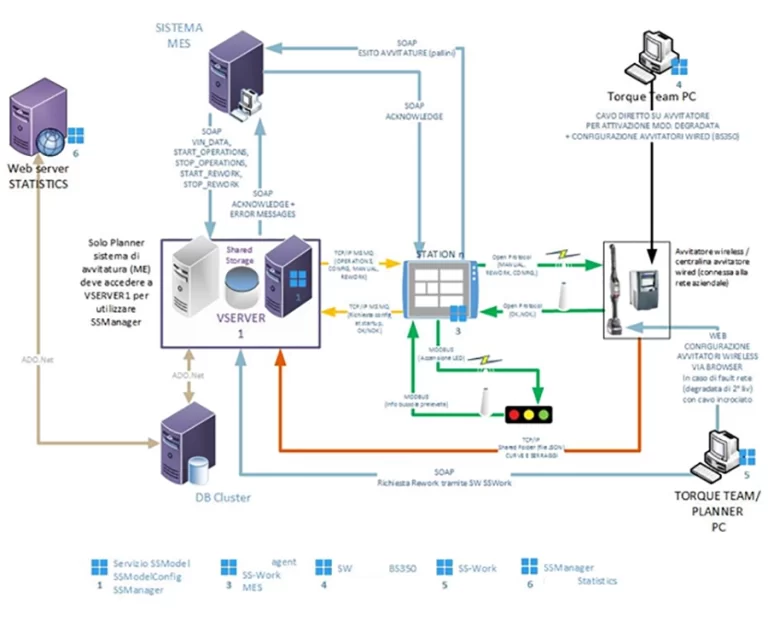
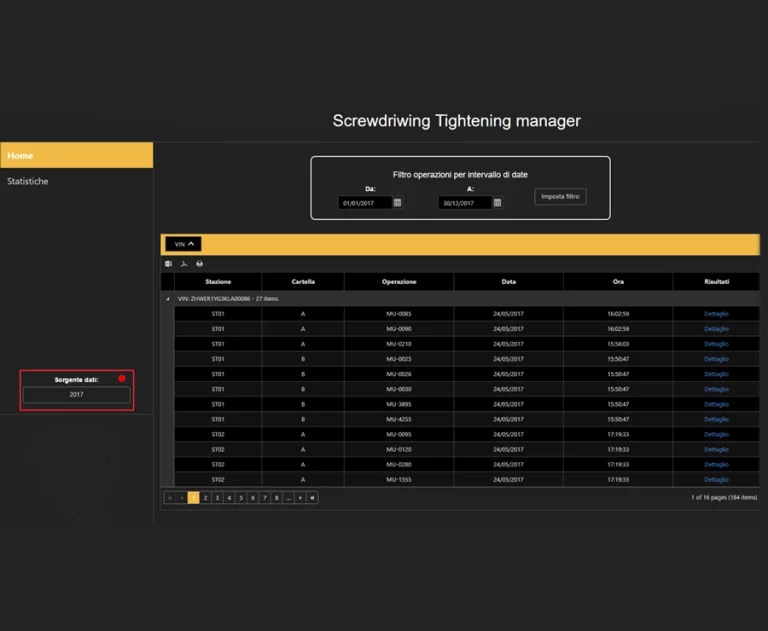
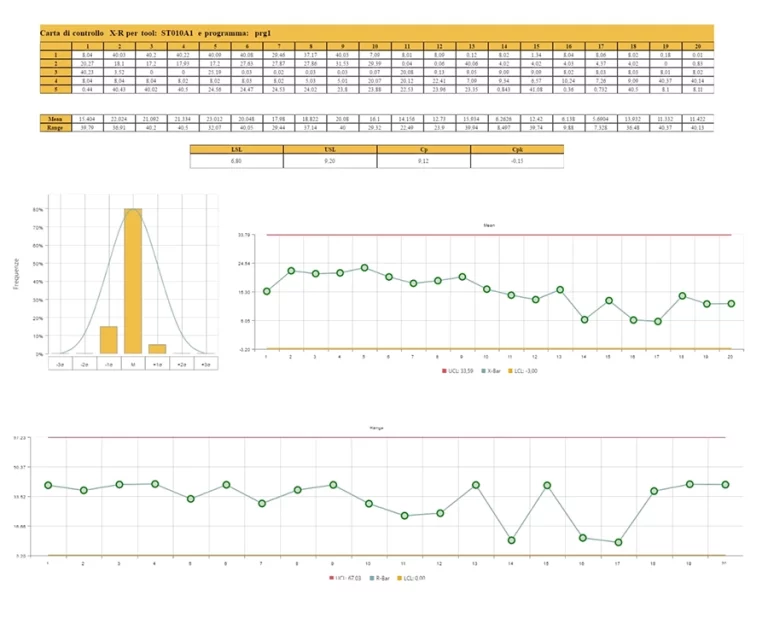
The system interfaces with the MES (Manufacturing Execution System) using torque/angle electronic screwdriving systems present on an automotive assembly line.
The MES sends the operation codes that need to be executed at each station of the line to the MODEL service’s Web Service. The MODEL service communicates to each FIELD the operations to be performed, any already acquired results, and the configuration of the devices at each station. At each station, the FIELD service activates a communication agent and, for each operation performed, sends feedback to the MES, which updates the operation information for the user on its front end.
The results of the operations and statistics can also be viewed through an intranet website. By viewing the X-R charts generated with the results obtained from the screwdriving devices, the torque team can identify any deviations and recalibrate the field devices as needed.
Technology: Windows Services, Windows Desktop, MS SQL Database, ASP Web, SOAP Web Services, SAP MES, BOSCH and ATLAS COPCO screwdrivers, Siemens PLC, OPC DA, MODBUS, TCP, scripting system with C# and VB .Net languages.
End-of-Line Control System
The readings taken by the measurement function are graphically represented in the central area of the Measurement View. The bar graph shows the error detected on individual sensors, while the polar graph visualizes the error of each acquisition relative to the diameter of the bar. The results are sent to the PLC, which interfaces with the line automation.
The system, with the aid of a series of precision probes, checks in various sections that the diameter of the bar is within tolerance.
Technology: Windows Desktop, MS SQL Database, Siemens PLC, OPC UA, National Instruments D/A boards
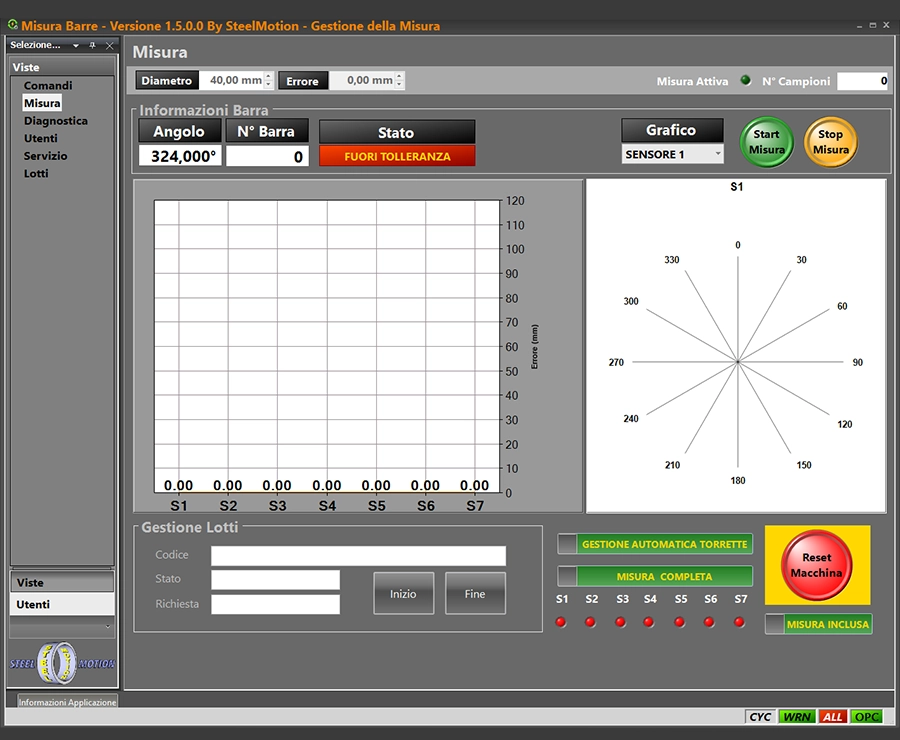
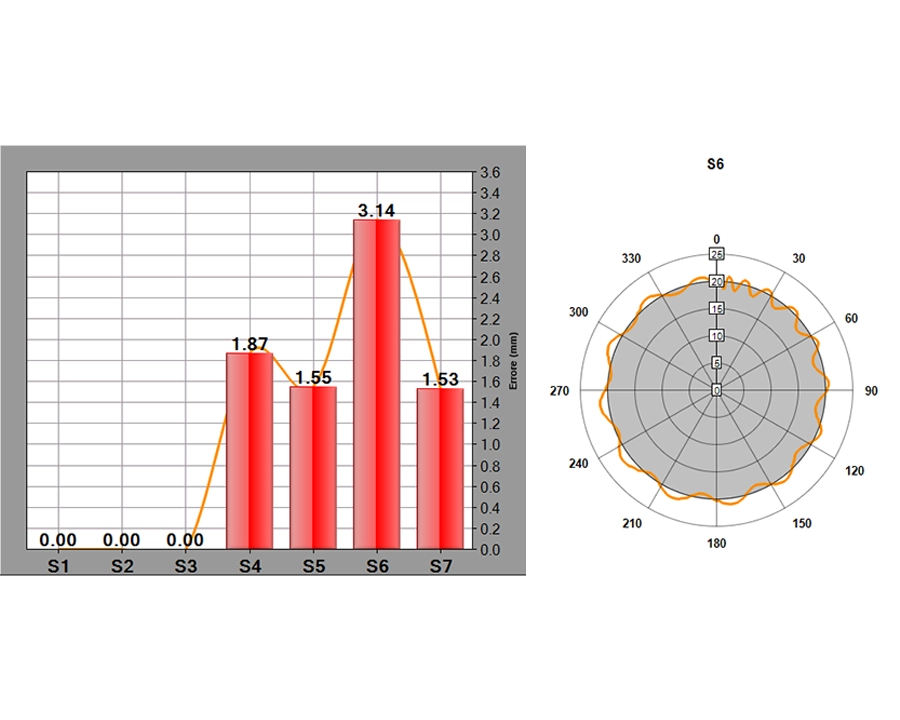
Guided Conduct System for Hydraulic Assembly
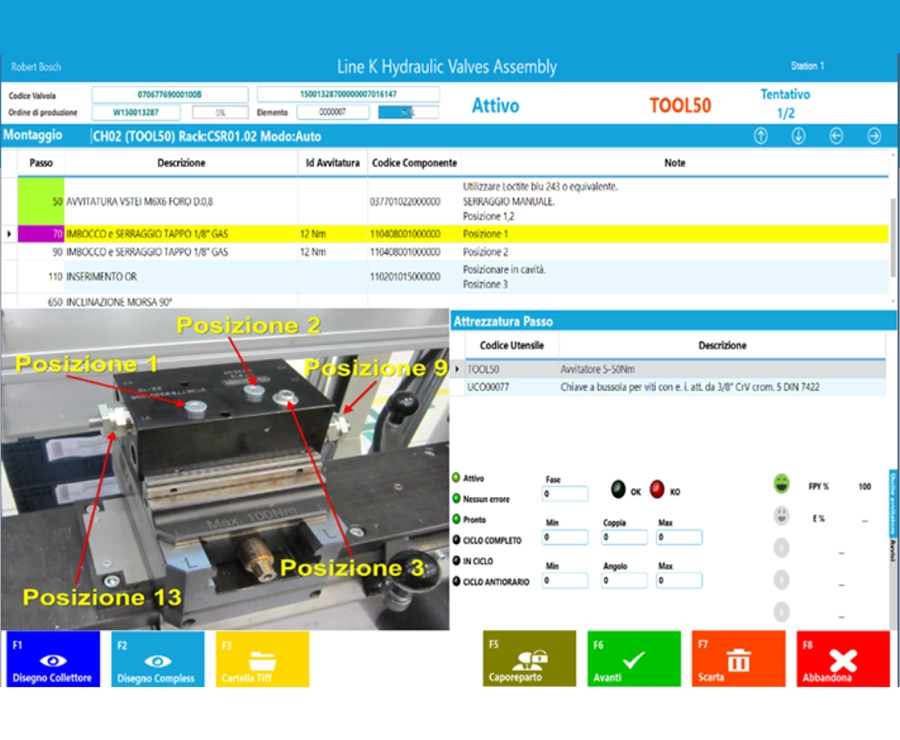
The application ensures that the operator performs all assembly operations in the predefined order. Each step of the operation is displayed to the operator in text form, possibly accompanied by a synoptic image. Operations can be either manual or automatic. Specifically, automatic operations can interface with various devices such as electronic screwdrivers, scales, pick-to-light systems, and digital I/O. The grid displays the list of steps coded in the assembly rule. The active step column is highlighted with a yellow text background. In particular, the Step column indicates the assembly step number and the operation status:
Active
Indicate the active assembly step
Complete
Indicates that the step has been executed
Faulty
Indicates that the step has not been completed and the component has been classified as defective. The workstation where the rejection occurred is excluded from the guided procedure
At the end of assembly, information for all pieces in the batch is stored in the central database. Accordingly, based on assembly results, the system provides the operator with a graphical feedback that assesses station productivity.

The most optimistic goal has been achieved

The minimum goal has been achieved

The minimum goal has not been achieved

The value cannot be calculated
Technology: MS SQL database, remote I/O BOSCH, OPC UA, RFID BALLUFF, BOSCH and ATLAS COPCO devices, BM Elettronica scale, INSPEKTO and COGNEX cameras, MODBUS, TCP
Maintenance Management System
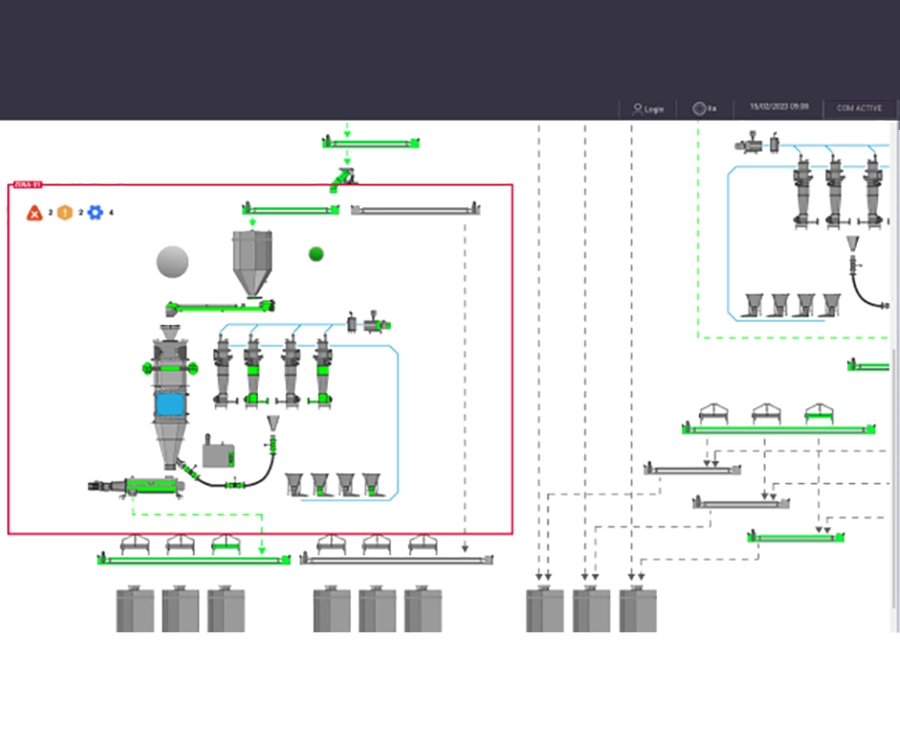
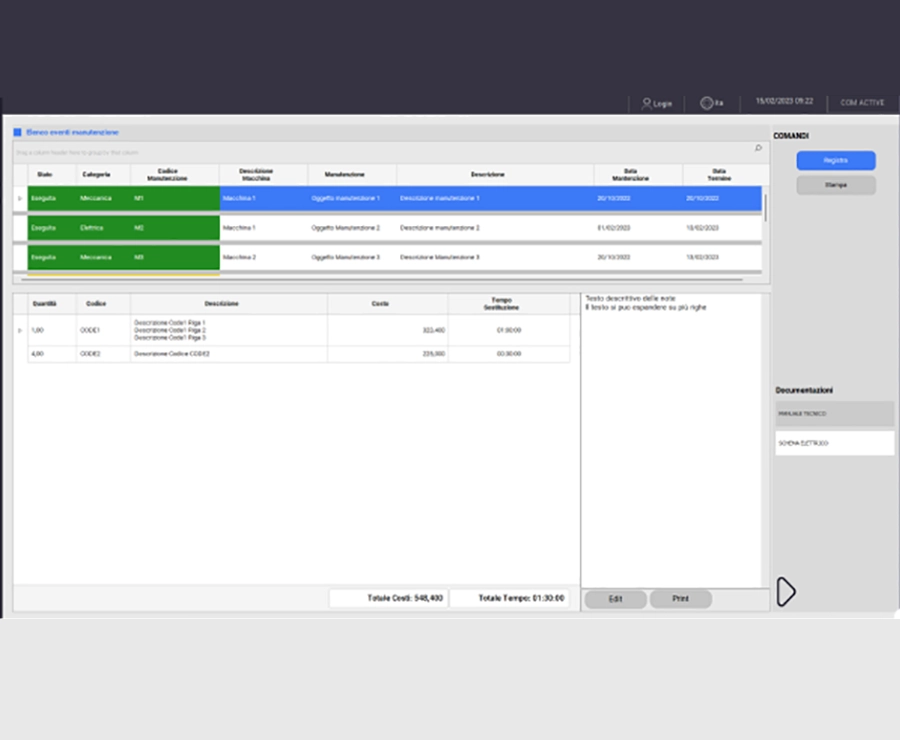
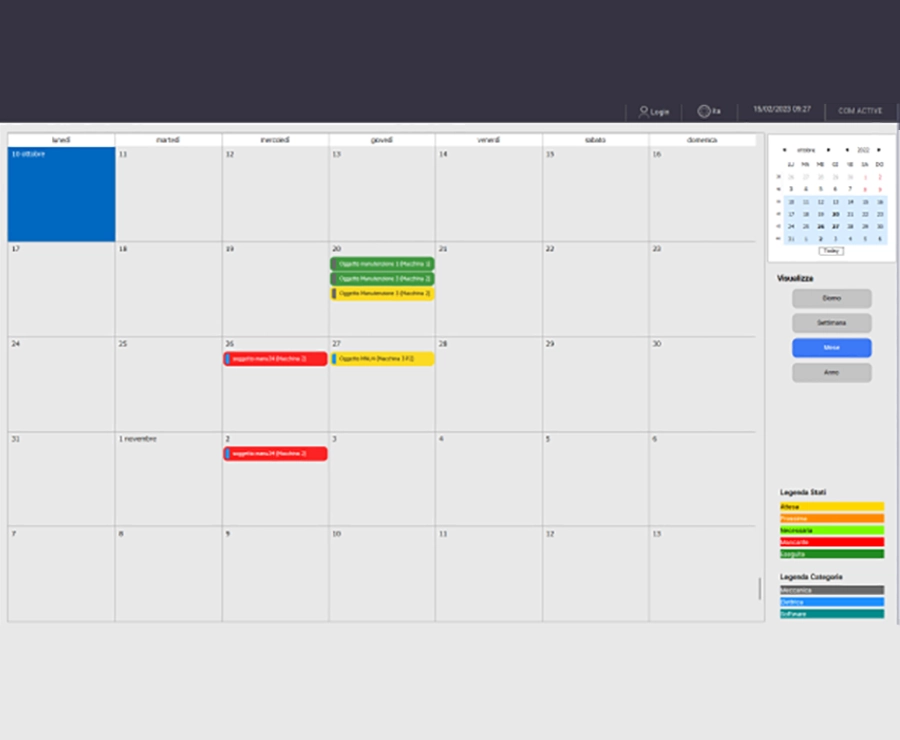
The system allows for planning and controlling maintenance interventions necessary for various machines in an industrial plant. These can be scheduled based on date or machine counters. Additionally, each maintenance task can be associated with a graphical widget that indicates the maintenance status in a mimic diagram. The mimic diagram can be simultaneously viewed on a desktop application or tablet.
Furthermore, the calendar page displays scheduled maintenance tasks on a weekly, monthly, or annual basis. For each machine or maintenance task, technical documentation is available, enabling maintenance personnel to understand the required operations and spare parts. The accessible documents include various formats such as PDFs, Word documents, Excel spreadsheets, images, and videos.
Maintenance records can include notes, spare parts costs, and time spent on various operations. Administrators have the ability to filter maintenance events and generate activity reports.
Technology: Windows Desktop, Windows Services, MS SQL Database, ASP.NET Core Web, Blazor Web Client, Dapper Framework, JavaScript, OPC UA.
A flat bar straightening machine
A flat bar straightening machine is designed to control a mechanical/hydraulic system capable of straightening rectangular bars of various sections to achieve the desired straightness per meter.
The straightening function of the machine is achieved by applying a force opposite to the measured deformation. Every body, or more precisely every isotropic continuous system subject to stress, deforms in proportion to the intensity of the applied force, the material’s nature, and other physical conditions. In general, elastic deformation disappears when the stress stops, otherwise, plastic or permanent deformation occurs. Specifically, there are materials that primarily undergo plastic deformation and materials that are elastic up to a certain stress value, beyond which plasticity occurs until failure.
To utilize corrective plastic deformation effectively, it is crucial for the machine to learn the mechanical behavior. To facilitate this learning process, the “Material Management” section includes a “Learning” card that allows for material characterization. Once the physical characteristics of the material are determined, the machine can correct bar deformations by measuring them at various sections and applying an appropriate correction logic.
Technology: Windows Desktop, MS SQL Database, OPC UA, Siemens PLC or Siemens CNC, Power MES, National Instruments D/A cards
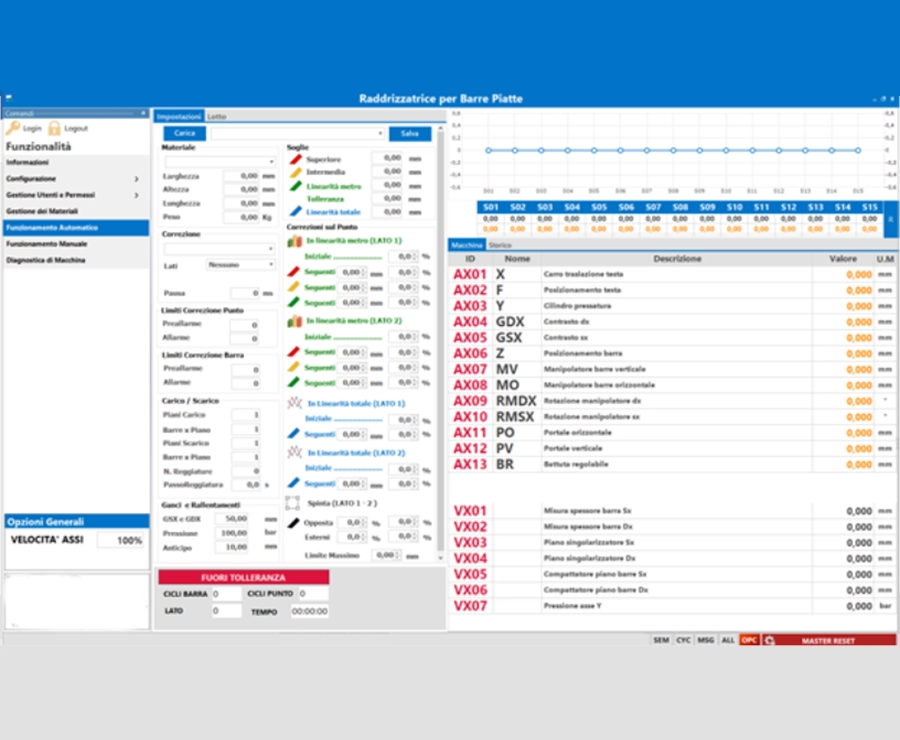
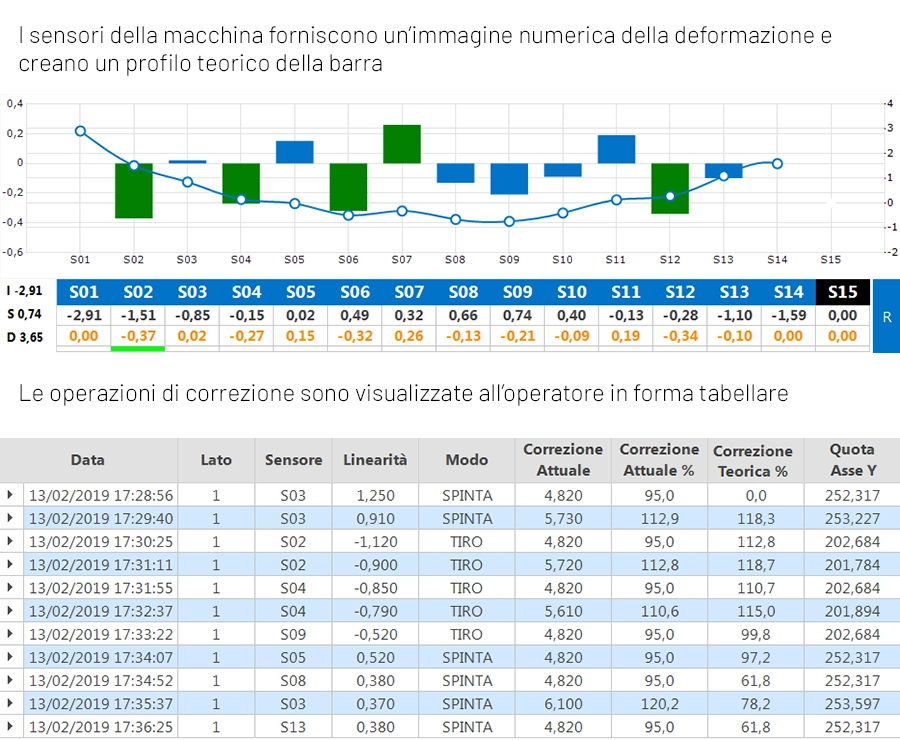
PLC and Motion Design
Infomotion boasts three decades of experience in developing software for automating machines and automatic production lines across diverse sectors such as packaging, food & beverage, ceramics, automotive, tobacco, logistics, medical, and more. Our goal is to leverage this expertise to serve both existing and potential clients by developing new projects and/or prototype machines, consolidating machines or production lines in operation, and providing ongoing support as needed.
The PLC software design leverages major development environments. Depending on the needs and requests of the client, we are capable of operating on various platforms, including:
Utilized in its latest version such as TIA Portal, it is employed for developing machines in the metalworking, packaging, and logistics sectors, as well as for servicing and modifications on older PLCs, using development environments like Step 7.
Known globally for its reliability, it is employed across various fields. Specifically, at Infomotion, we primarily use it in the packaging and logistics sectors, as well as in more niche areas such as glass and transportation of plastics.
A PLC with immense performance capabilities and extensive programming possibilities, open to the development of various software layers thanks to its comprehensive support for proprietary libraries, provided by the TwinCAT development environment.
A platform that has been gaining traction in recent years, particularly in applications that demand high-performance motion capabilities.
In addition, within our team, we have experienced professionals capable of developing on less common platforms such as Schneider, Omron, and Bosch.
In recent years, the evolution of automatic machines has led to a transition from predominantly mechanical machinery to systems where the electronic component is becoming increasingly significant. This shift has brought about greater flexibility in format changes, reduced mechanical maintenance needs, lower associated costs, and increased productivity. Electronic cams, synchronous control and activation of controlled movements, and vision systems are now commonplace.
This demand has driven PLC manufacturers to integrate motion control instructions into their systems.
Revamping obsolete machines presents a crucial opportunity for businesses to maintain competitiveness in the global market. That’s why Infomotion has acquired expertise over the years to support clients in transitioning to these types of machines, assisting in converting old mechanical cams to electronic ones.
Our development department is structured to meet client needs by providing customized solutions, starting from preliminary project studies and following functional specifications provided by companies or agreed upon jointly. We then focus on electrical design to find the most efficient and effective solution for specified requirements, ensuring reliability, safety, excellent scalability, and timely and cost-effective project completion.